About Me
My name is Marc Brooker. I've been writing code, reading code, and living vicariously through computers for as long as I can remember. I like to build things that work. I also dabble in machining, welding, cooking and skiing.
I'm currently an engineer at Amazon Web Services (AWS) in Seattle, where I work on databases, serverless, and serverless databases. Before that, I worked on EC2 and EBS.
All opinions are my own.
This is my less-technical blog on non-work topics. For my main blog, visit
https://brooker.co.za/blog/.
Links
My Publications and Videos
@marcbrooker on Mastodon
@MarcJBrooker on Twitter
Review: Tormach PCNC 440
It's a little CNC mill.
Bottom line: It’s a solid little 200kg-ish CNC mill that works like you’d expect a 200kg mill to work. It doesn’t work like a 2000kg mill. It cuts real parts out of real metal.
Back in 2020, just before the event1, I bought a Tormach PCNC 440 CNC mill to add to my shop. After buying it, I learned that these things are super controversial. There’s more than one machining forum that’ll outright ban you for mentioning you own one. You’ll find folks saying that they don’t work at all, that they’re only good for plastic, can’t hold tolerances, or won’t cut steel. After having owned one for about four years, I don’t see what the fuss is about. I like it. It’s a little mill that performs like a little mill. If you expect it to do the things a million-dollar four-tonne machine can do, you’ll be disappointed. But if you want to make parts in aluminium, steel, brass, or even stainless that can be made with 1/4” (6mm) or smaller tooling, you’ll probably be happy.
Pros
- I’ve cut wood, plastic, brass, bronze, aluminium, mild steel, tool steel, stainless steel, and even nasty air-hardening stainless tool steel2 with mine. With some care given to feeds and speeds, I’ve had no problem with any of these materials.
- I’ve been able to hold good tolerances (down to 25μm/0.001”) and get good repeatability. Light finish passes are sometimes needed that wouldn’t be needed on a bigger machine.
- PathPilot (the UI) is solid. The conversational programming interface is pretty basic, but does the important stuff and is super easy to use. I like the built-in probing, interactive 3D gcode preview, and simple tool library management.
- PathPilot runs on a regular PC running Linux, so it’s super easy and cheap to accessorize (I added a touch screen and wired LAN, for example). It also doesn’t come with the memory or storage limits that some ‘classic’ controllers come with.
- The Tormach Tooling System (TTS) is adequate for this size machine, and makes it super easy to make custom tools (without having to perfectly match a machine taper).
- The pneumatic power drawbar system is super convenient and easy to use.
- Decent 1/4” carbide tooling is pretty cheap (e.g. from Lakeshore Carbide or Shars). Other smallish tools like thin slitting saws and fly cutters work great too.
- The spindle goes up to 10,000 RPM and down to a few hundred. This range makes it easy to use small tools, while still being able to drill. There are two physical ranges (with a belt), and within those ranges the control is continuous.
- The fogbuster coolant system works well, and makes it easy to choose between mist cooling and just an air blast to clear chips.
- I got the fourth axis, and it’s a great little thing. Simultaneous fourth axis machining works well. Cheap CAM options are limited so I often end up writing my own code that generates GCode.
- It fits in my shop. I have a low ceiling (2.1m), so I couldn’t have a Haas or Brother or something even if I wanted to. I can’t even fit a decent knee mill in, but that’s a different problem.
Cons
- It’s a 200kg machine, and about as rigid as one could expect a 200kg machine to be. You’re not going to be hogging out steel with a 1” endmill on this machine.
- The limited rigidity means limited tool diameters (mostly 1/4” or up to 3/8”), which also means limited length of cut, making some parts harder to make.
- It sucks at drilling with bigger (>10mm) drills. The whole path (spindle motor, belt, TTS) just don’t have enough torque to do drive big drills at their optimal speeds and feeds. I mostly make up for this by interpolating holes with an endmill and then reaming to final size.
- The envelope is quite limited in size, especially in Y. There’s plenty of Z space for the stuff I do, but if I did more castings I’d probably want more.
- The material removal rate in steel isn’t great. That’s not a problem for me at all, but would mean it’s a poor choice for a production shop.
- The touch probe is a great feature, and works really nicely most of the time, but needs frequent recalibration.
- I wish PathPilot was a little more extendable/customizable without having to throw it out (in favor of LinuxCNC or Mach or something) entirely. In particular, I’d like some surface mapping routines, SVG engraving, and automatic support for the “interpolate-then-ream” workflow.
Stuff I’ve Made
This is a small sample of the stuff I’ve made on the Tormach. I’ve made a bunch of other things, including machine parts, a few Hemingway Kits, and a bunch of small gifts on the machine too.
A small prize for somebody at work, in aluminium and walnut.
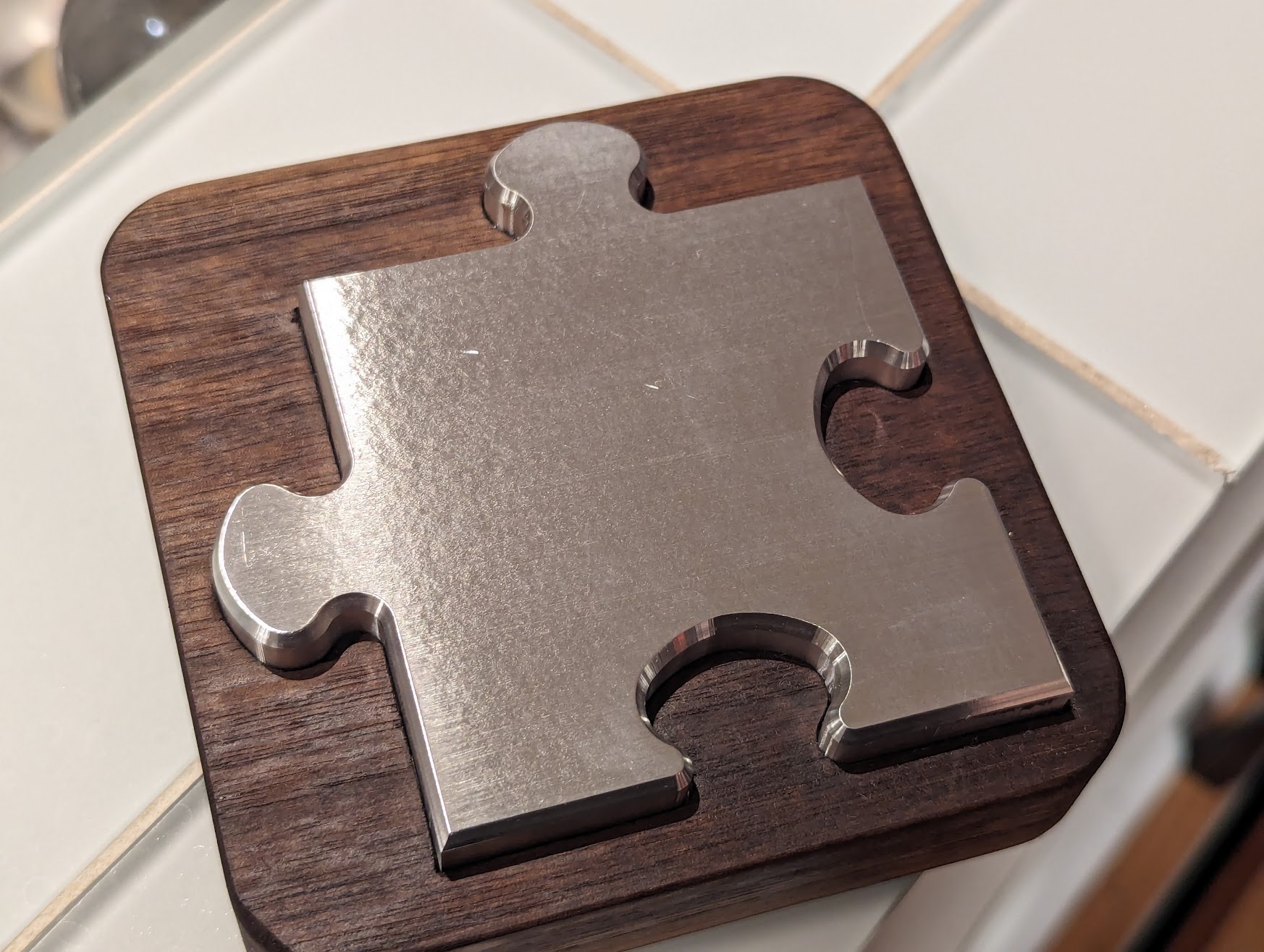
Star Trek: Strange New Worlds badge keyring (in silicon bronze).
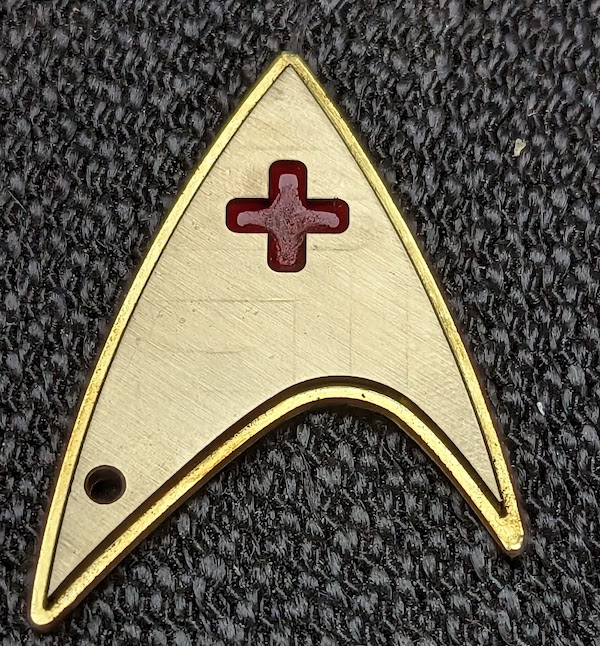
Custom Knurls (for the Hemingway Sensitive Knurler, which I also made on the Tormach), in O1 and A2 tool steels. This is a simultaneous fourth axis operation.
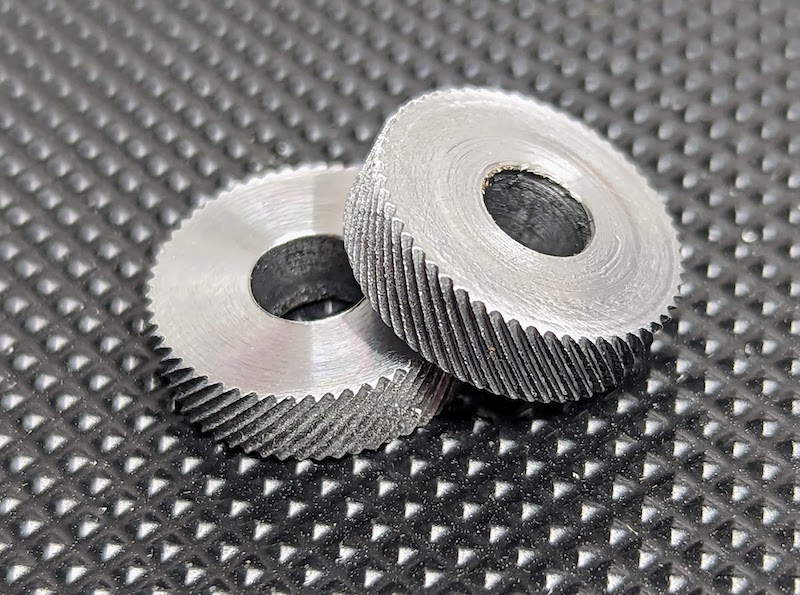
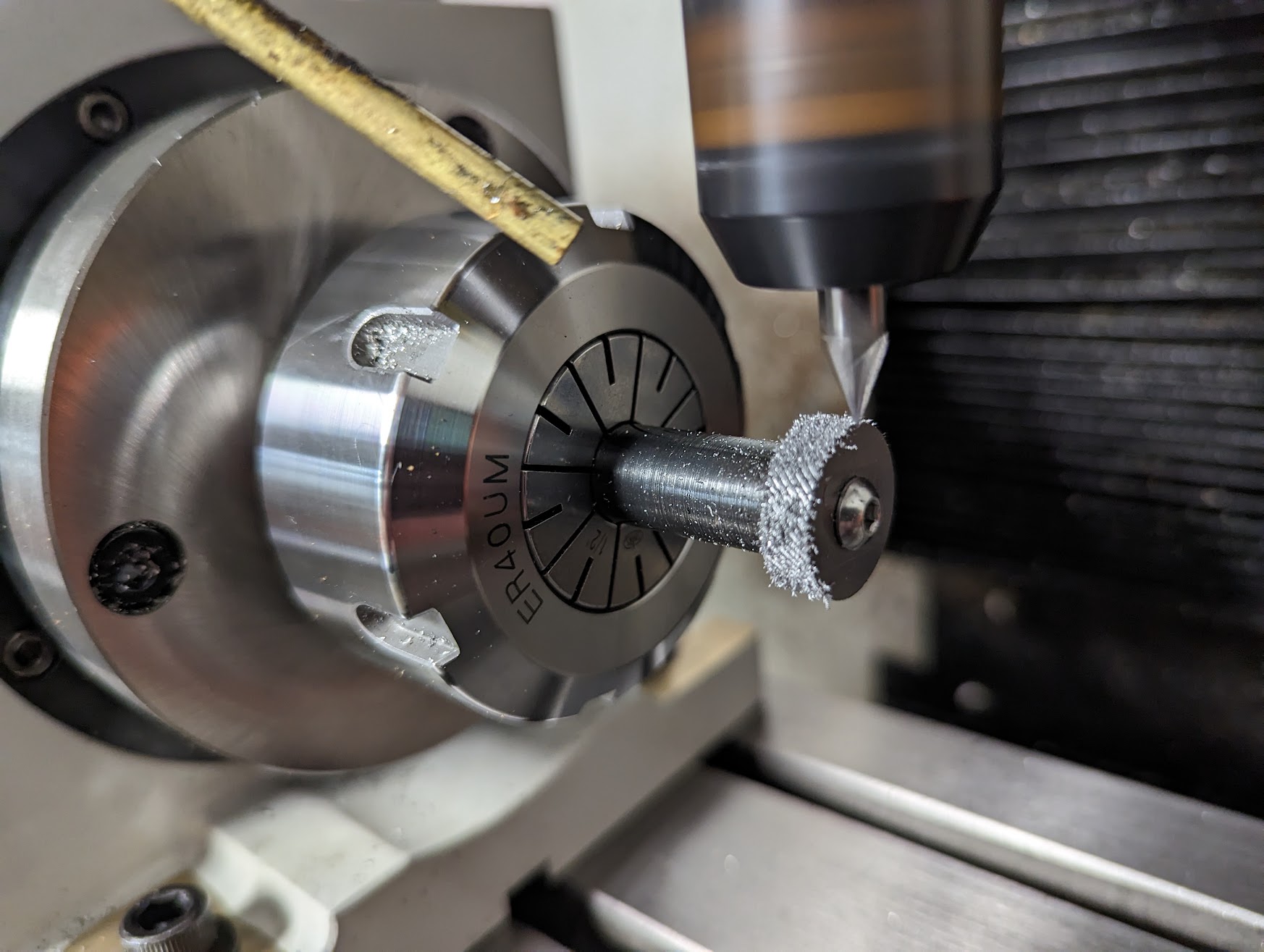
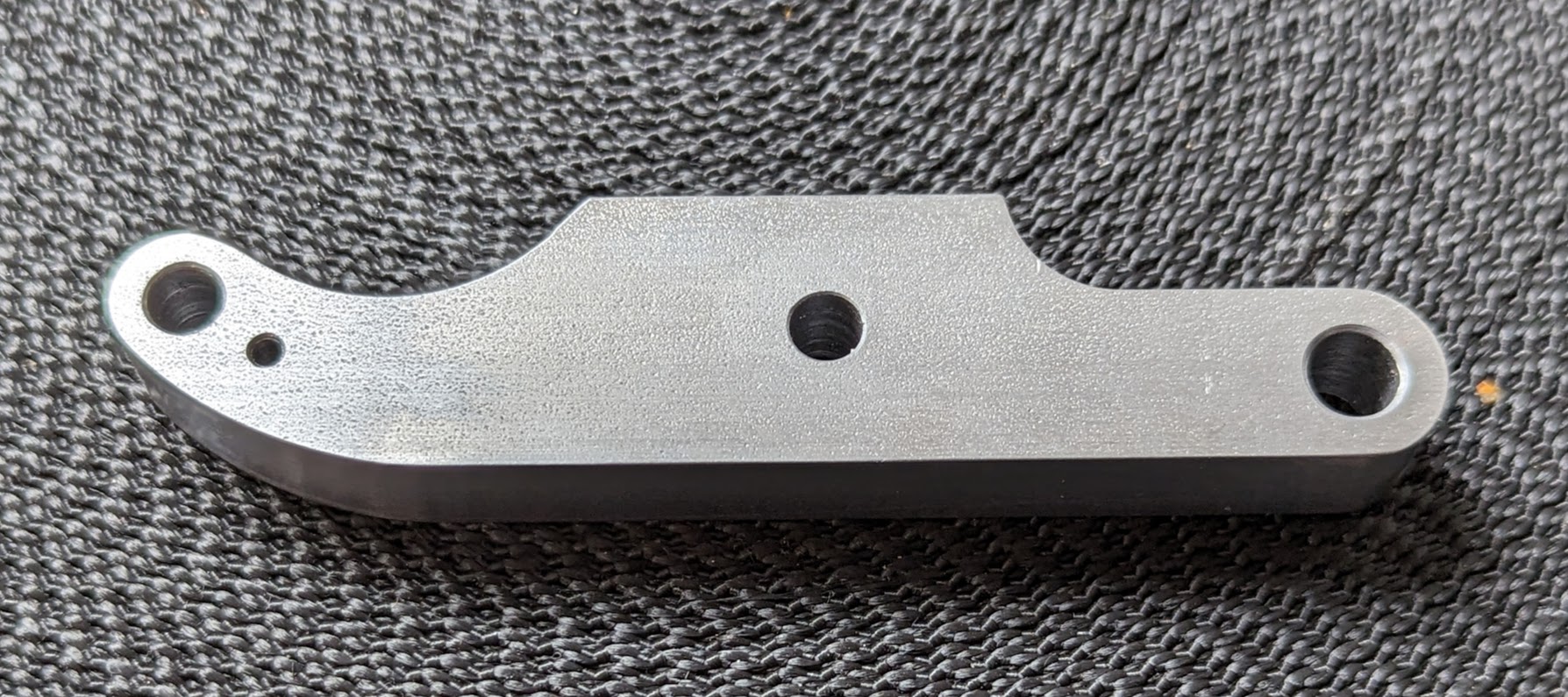
Some “carved” details for furniture, in cherry wood.
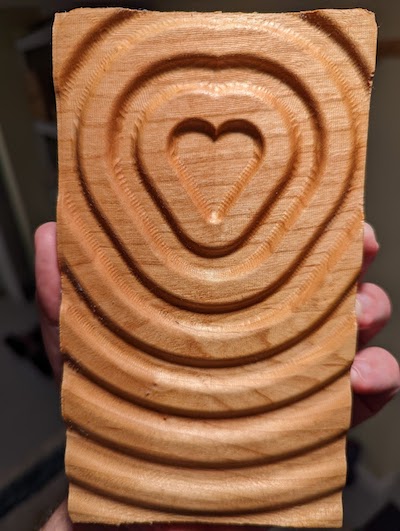
Pieces for a custom Quarto set for my wife’s birthday, in silicon bronze and 316 stainless (the round ones were turned, but the square ones and all the pocketing are done on the Tormach).
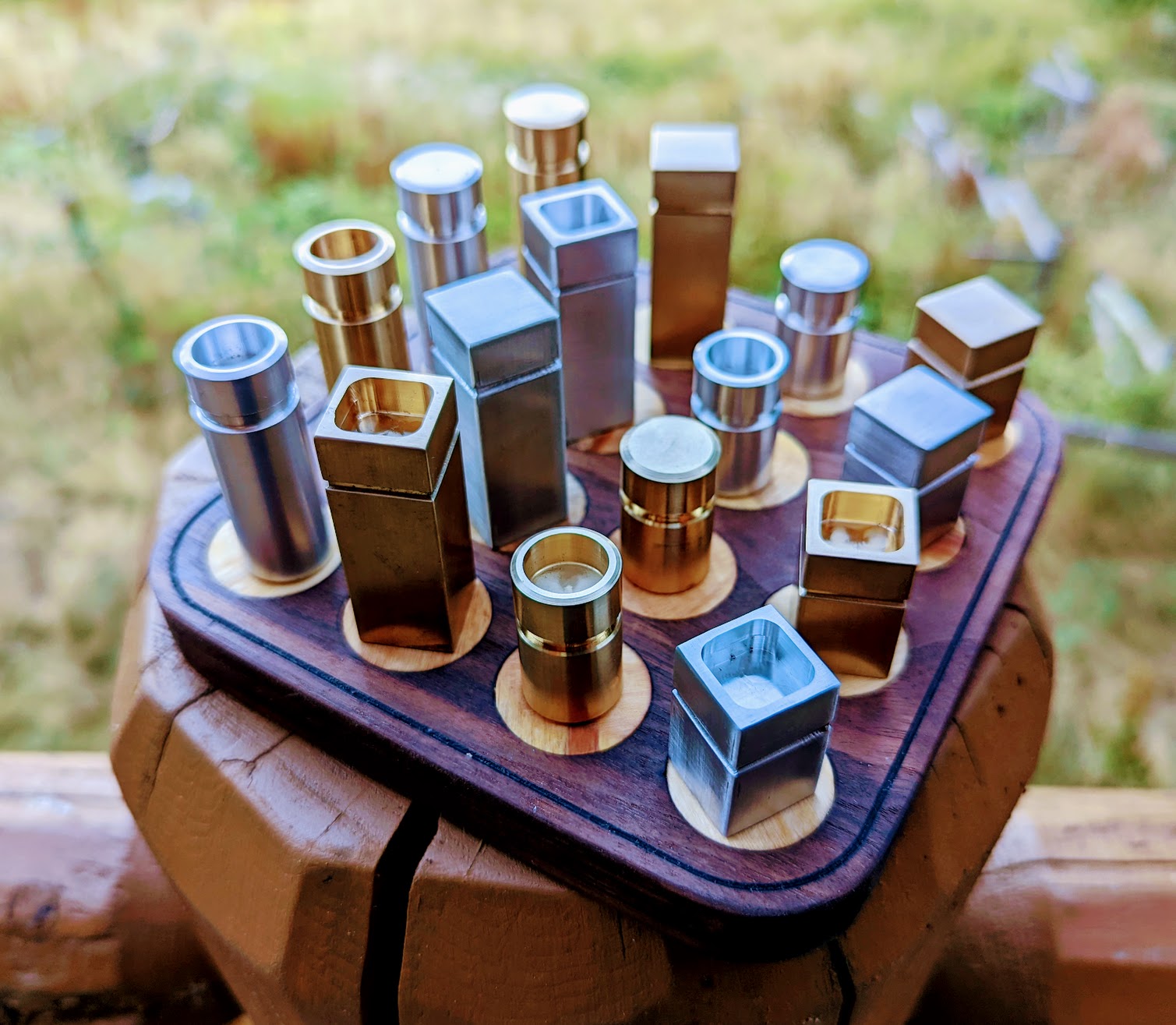
Slotting S90V, a particularly nasty Vanadium-rich stainless.
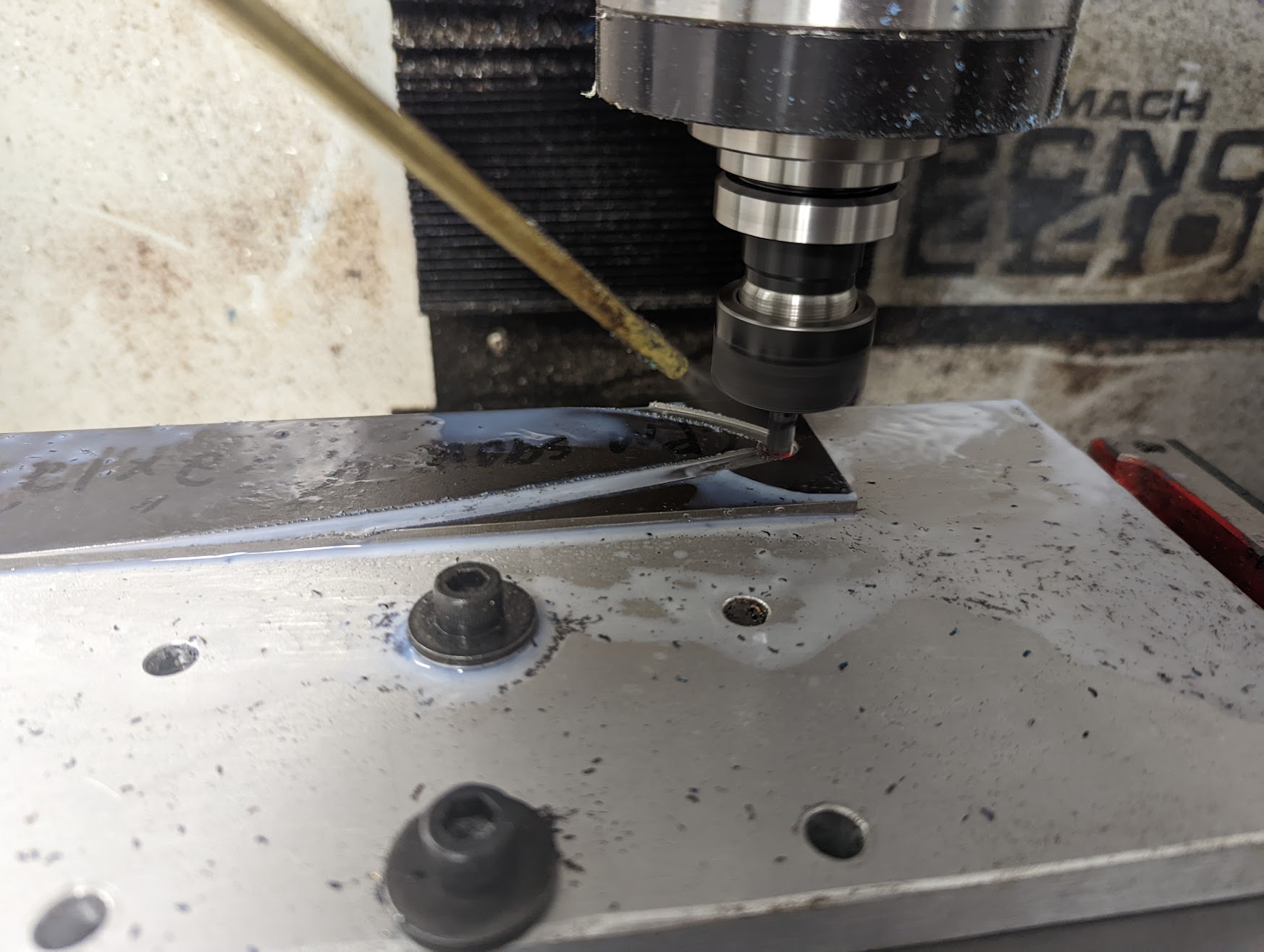
Footnotes
- Remain indoors.
- Curse you, S45VN! Great for knives, awful to machine.